
ALPHA PROTOTYPE
Background:
Team Acero was tasked with creating a device capable of creating clear ice easily for consumer use without tedious specialized procedures required. Clear ice makers that make quality high clarity ice are widely available on the market but in an industrial sense. The clear ice makers that are available to purchase and are consumer based do work but does not produce high clarity and quality clear ice and are ridiculed with impurities making the resulting ice cloudy in appearance and occasionally has imperfections on the surface. Prior to beginning the design and manufacturing process, there were functional requirements created to gauge feasibility and practicality of this concept. The functional requirements that had to be met are listed below.
​
Functional Requirements to Meet:
1. The device with dimensions of 7.5 x 7.5 x 8.5 inches should fit within a standard commercial small to medium sized freezer.
2. Produce clear ice with high clarity quality and transparency.
3. Device should not cost more than $50 to manufacture
4. Desired ice to be easily separable from other formed ice within the device and easily extractable from ice mold.

Picture 1:
​
Exploded view of the individual components for the clear ice cooler assembly. The following parts are:
1. Ice Cube Mold
2. Mold Separator
3. Inner Shell
4. Insulation
5. Outer Shell
​

Picture 2:
​
CAD cross sectional view of the clear ice maker assembly with all components



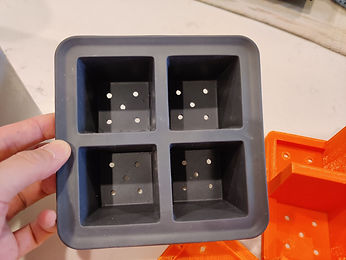
Picture 3:
​
CAD mold model seen on the left vs actual silicone mold on the right. 20 holes created to align with separator holes to allow for water flow and sediment exits

Picture 4:
​
Separator modeled in CAD seen on the left vs 3D printed separator on the right. Left 3D printed separator made with PETG vs PLA on the right
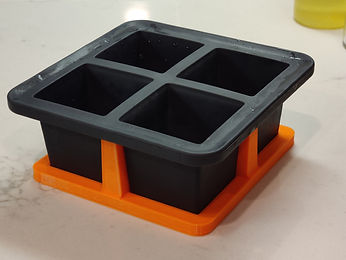
Picture 5:
​
CAD generated separator model attached with mold. Actual 3D printed separator with ice cube mold that fits snugly within separator piece component seen on the right
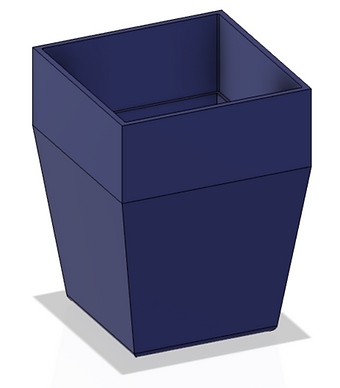

Picture 6:
​
Inner shell generated in CAD versus actual 3D printed inner shell using PETG filament (orange separator seen inside inner shell)

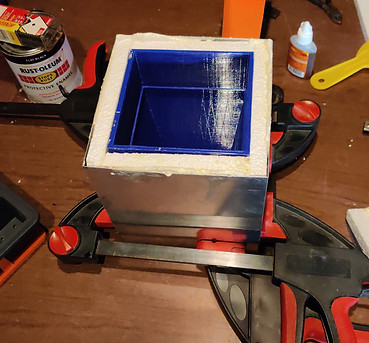
Picture 7:
​
CAD insulation modeled on the left. Expanded polystyrene foam boards assembled using gorilla glue and clamps seen on the right. Inner shell was placed inside to hold the shape when glue was curing.

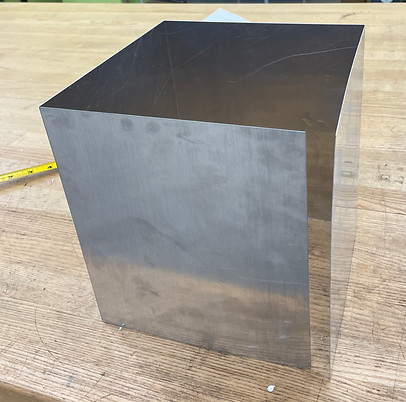
Picture 8:
​
Outer shell modeled in CAD on the left versus 1/32 inch aluminum sheet metal bended to general shape on the right


Picture 9:
​
Alpha prototype modeled in CAD versus actual final alpha prototype manufactured with all the previously mentioned components seen on the right.

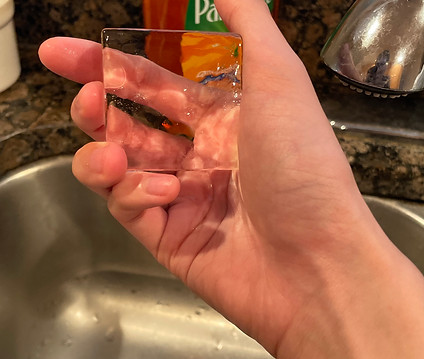
Picture 10:
​
Final alpha prototype clear ice cooler tested in standard small commercial freezer pictured on the left. Resulting clear ice produced pictured on the right. The yielded ice was high in visual clarity and quality with 0 to none impurities with full transparency proving to be a sufficient means as to create clear ice for consumer use.